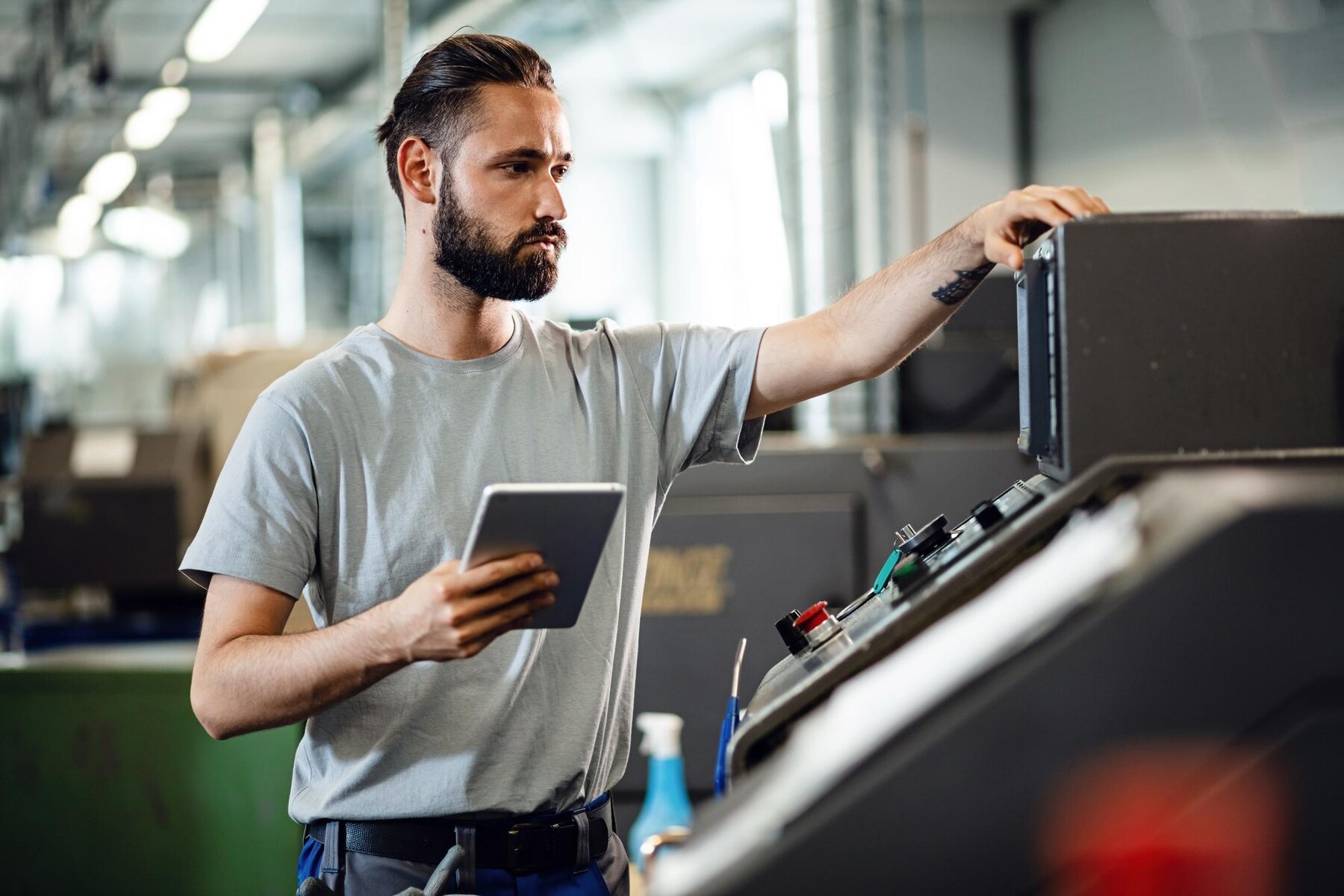
¿Te gustaría acabar con la sobreproducción, los altos tiempos de espera y los desperfectos en los productos?
Gracias al Lean Manufacturing puedes conseguirlo. Y es que esta nueva metodología de gestión permite aprovechar al máximo tus recursos y reducir los costes de producción sin comprometer la calidad del producto.
¿Qué es Lean Manufacturing?
El Lean Manufacturing es una filosofía degestión del trabajo que se enfoca en satisfacer las expectativas del cliente minimizando el desperdicio. Es decir, eliminando todos aquellos procesos o actividades que no añaden valor al producto final.
De manera que, al igual que las metodologías ágiles, se trata de una cultura empresarial flexible que persigue la mejora continua en la producción.
Esta metodología tiene su origen en el Sistema de Producción de Toyota, desarrollado por la empresa automotriz japonesa después de la Segunda Guerra Mundial, y se rige por los siguientes principios:
Identificación del valor
En la primera fase del Lean Manufacturing se debe determinar qué es lo que el cliente realmente valora del producto o servicio. Lo cual implica comprender las necesidades y las expectativas del cliente para poder enfocar todos los esfuerzos en esa dirección.
Este enfoque permite emplear los recursos de manera más eficiente para satisfacer al cliente y, al mismo tiempo, mejorar la competitividad de la empresa.
Mapeo de la cadena de valor
La segunda fase del Lean Manufacturing consiste en analizar todos los pasos del proceso de producción para identificar y eliminar desperdicios.
Este mapeo visualiza el flujo de materiales desde la materia prima hasta el producto final, permitiendo identificar las actividades que no añaden valor, como las esperas, los transportes innecesarios o los excesos de inventario, con el objetivo de optimizar cada paso para que contribuya directamente a la creación de valor.
Flujo continuo
Para maximizar la eficiencia, es necesario asegurar que el proceso de producción fluya sin interrupciones. Y, justamente, en eso consiste la tercera fase del Lean Manufacturing. Un flujo continuo minimiza el tiempo de espera y los cuellos de botella, lo que se traduce en una producción más rápida y con menos desperdicio.
Producción pull
En lugar de producir grandes cantidades de producto que posteriormente serán almacenados, el Lean Manufacturing se basa en producir solo lo que se necesita, cuando se necesita.
Este enfoque reduce los inventarios y asegura que los recursos se utilizan de manera eficiente, respondiendo directamente a la demanda real del cliente. La metodología Kanban es fundamental para implementar este sistema, ya que permite visualizar y gestionar el flujo de trabajo de manera efectiva.
Mejora continua
Fomentar una cultura de mejora constante en todos los niveles de la organizaciónes crucial para el éxito del Lean Manufacturing. Pues la filosofía Kaizen implica la participación de todos los empleados en la identificación y solución de problemas, promoviendo cambios pequeños pero continuos que mejoren los procesos.
Como ves, adoptar el Lean Manufacturing representa un cambio de mentalidad que conlleva pasar de la fabricación de productos a la creación de soluciones. Y este cambio de enfoque tiene múltiples beneficios para las empresas.
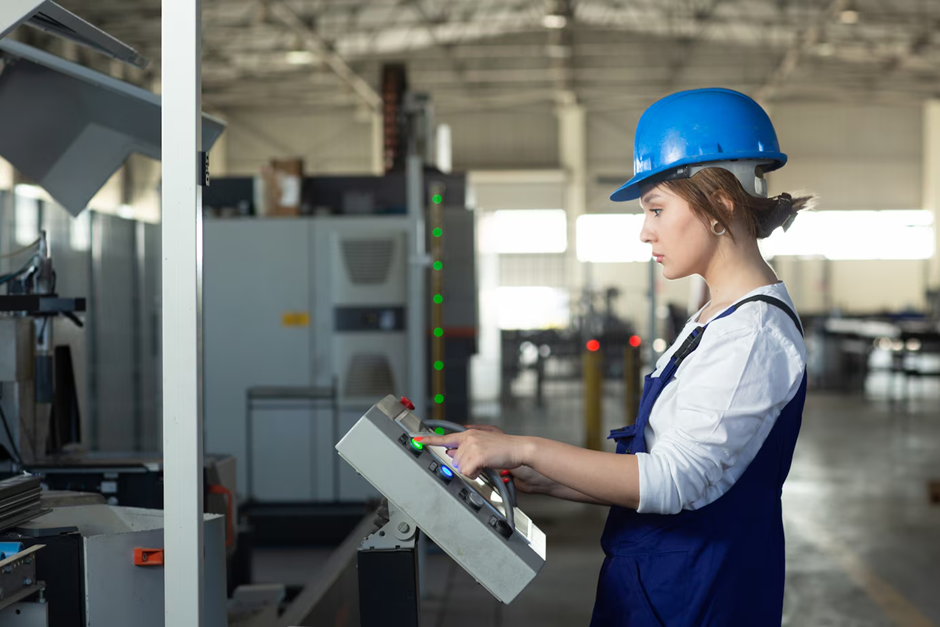
Beneficios de aplicar Lean Manufacturing en tu empresa
Apostar por el Lean Manufacturing, puede ser la clave para asegurar el crecimiento y la sostenibilidad en el tiempo de las empresas a largo plazo. Sin embargo, si nos centramos en lo más inmediato, son muchos los beneficios que esta metodología puede ofrecer:
- Reducción de costes: Al eliminar desperdicios y optimizar procesos, los costes de producción disminuyen significativamente. Lo cual no solo reduce el gasto general, sino que también libera recursos que pueden ser reinvertidos en otras áreas de la empresa para fomentar su crecimiento.
- Aumento de eficiencia: Los procesos se vuelven más ágiles y eficientes, mejorando la productividad general de la empresa. Esto permite realizar más trabajo con menos recursos, aumentando así la capacidad de producción sin necesidad de grandes inversiones en infraestructura.
- Mejora de la calidad: Al centrarse en lo que aporta valor al cliente, disminuyen los defectos y mejora la calidad del producto final. Además, la atención a los detalles y la corrección constante de errores garantizan un producto superior que satisface con creces las expectativas del cliente.
- Incremento de ventas: Los productos de mayor calidad y los tiempos de entrega más cortos contribuyen a incrementar la satisfacción del cliente y, como consecuencia, las ventas. Pues cuando un cliente recibe un producto que cumple o supera sus expectativas, su lealtad hacia la empresa aumenta. Lo que puede traducirse en repetición de negocios y recomendaciones positivas.
- Flexibilidad y adaptabilidad: La filosofía Lean Manufacturing permite a las empresas adaptarse rápidamente a los cambios en la demanda del mercado. Una flexibilidad que resulta crucial para responder con agilidad a nuevas oportunidades o amenazas, manteniendo su relevancia y competitividad.
Ahora bien, para poder conseguir estos objetivos, es necesario contar con las herramientas adecuadas.
Herramientas y técnicas de Lean Manufacturing
El listado de las herramientas y técnicas que pueden facilitar la implementación del sistema Lean Manufacturing podría ser interminable. No obstante, en este artículo, solo vamos a nombrar las más utilizadas:
1. 5S: esta técnica se centra en cinco principios japoneses (Seiri, Seiton, Seiso, Seiketsu y Shitsuke) que buscan mejorar la organización y la eficiencia en el lugar de trabajo.
2. JIT (Just-in-Time): esta metodología asegura que los materiales y productos se entreguen justo a tiempo para su uso, reduciendo inventarios y costos de almacenamiento.
3. Kanban: técnica de programación visual que ayuda a gestionar y mejorar el flujo de trabajo a través de tarjetas visuales que facilitan la agilidad en la gestión de proyectos.
4.Poka-Yoke: esta técnica se enfoca en la prevención de errores mediante la implementación de mecanismos a prueba de fallos en los procesos de producción.
5. TQM (Total Quality Management): gestión de la calidad total que se enfoca en la mejora continua de los procesos, productos y servicios con el objetivo de aumentar la satisfacción del cliente.
6. RPA (Robotic Process Automation): automatización de procesos robóticos, que utiliza software para realizar tareas repetitivas y basadas en reglas, mejorando la eficiencia y reduciendo errores.
7. TOC (Theory of Constraints): la teoría de las restricciones se centra en identificar y gestionar los cuellos de botella en los procesos de producción para maximizar el rendimiento.
8. Andon: sistema de alerta visual que indica el estado de la producción en tiempo real, permitiendo la rápida identificación y resolución de problemas.
9. SMED (Single Minute Exchange of Die): técnica que busca reducir el tiempo de cambio de herramientas o ajustes en máquinas, aumentando la flexibilidad y eficiencia de la producción.
Si estás buscando nuevas formas de trabajar para aumentar la eficiencia y la productividad de tus empleados, te sugerimos que revises nuestros cursos sobre gestión de proyectos. En ellos, encontrarás diferentes metodologías que te ayudarán a mejorar la competitividad de tu empresa y a asegurar su continuidad a largo plazo.